CMC RVS
The market for polyurethanes has undergone a substantial change in recent years due to the migration of the production to low wage areas. For this reason, operators have concentrated their energies in finding production solutions with high technological content and low environmental impact employing traditional and new types of polyurethanes. The technology of spray polyurethane performed alone or combined with other processes, has opened broad prospects for the production of new products, solving current and future construction issues and eliminating costly production steps currently present in traditional production. To have a better idea of the use of spray polyurethane technology, we list some applications:
- Rigid structural spray combined with low density injected polyurethane
Insulated product with a high mechanical strength of the surface.
- Structural rigid spray combined with medium density injected polyurethane
Carrier product with high mechanical strength of the surface.
- Structural rigid spray applied to rigidly shaped conglomerates
Carrier product with high mechanical strength of the surface.
- Flexible spray combined with medium density cast polyurethane
Carrier product with a soft contact surface.
- Flexible spray combined with flexible cast polyurethane
Flexible product with soft surface with high mechanical and weathering resistance.
- Flexible spray applied to pre-shaped flexible conglomerates
Flexible product with soft surface and high mechanical and weathering resistance.
The low pressure CMC RVS Mixers are designed using modern technologies adapting them to the needs of all types of user.
Key benefits
- Simplicity of use
- Reliability
- Flexibility
- Low maintenance
- Complete customization
Dosage of components
- Volumetric metering pumps with high precision double gear
- Variable flow by meter
- Digital pressure regulators sensing component dosing pressure
- Suction filter dosing pump
Storage and conditioning components
- Component tanks with external cavities for recycling cooling liquid, capacity: 30 Lt
- Slow gate paddle agitator scraper on tank bottom to lift any decanted material or color
- Automatic temperature control components using electrical resistance
- Visual levels on component tanks
- Signaling levels component backup
- Valves for washing and discharge lines of component tanks cleaning
Component mixing
- Mixing gun with component recycling
- Automatic recycling and casting pressures
- Static mixers with air envelope spray nozzle
- Calibration of the components directly from the mixing gun
Machine control
- Touch screen for the control and display of the machine functions to guide the user through the choice of the programs to be set
- Machine cycles: CALIBRATION, WORK
OPTIONAL
- CMCCPI
Component flow controllers for the display of the total flow values, and of the single components and the testing of the mixing ratios
- CMCLCC
Level of charge of anti-crystallization components
- CMCUS
Spray jets available 1, 2, 3.
- CMCPRO
Diaphragm pumps for loading components complete with suction tube
- CMCGMPD
Magnetic coupling drive for dispensing pumps to eliminate completely component leaking due to seal wear
- CMCR
Roving fiber cutting for polyurethane foam reinforcement
- CMCBS
Special head holder arm following customer request
|
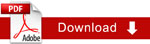 Depliant download (pdf 740Kb)
|